FAQs
Certificates
Which magnet coatings are there?
Table of Contents
Neodymium magnets (super magnets): Coating necessary
Nickel (Ni-Cu-Ni)
Gold-coating (Ni-Cu-Ni-Au)
Chrome (Ni-Cu-Ni-Cr)
Copper (Ni-Cu)
Epoxy resin (Ni-Cu-Ni-Epoxy)
Zinc (Zn)
Pot magnets
Special coatings
Ferrite magnets: No coating
Neodymium magnets (super magnets): Coating necessary
Neodymium reacts to oxygen and oxidises quickly if untreated. That's why all neodymium magnets in our shop are covered with a protective coating, which is so thin that it doesn't have any impact on the adhesive force of the magnet.
We use the following coatings on our neodymium magnets:
Nickel (Ni-Cu-Ni)
By far the most frequently used coating
Colour: shiny metallic
Good price/performance ratio
Thickness: approx. 12 micro metres
Gold-coating (Ni-Cu-Ni-Au)
Razor-thin coating (24k) over normal Ni-Cu-Ni coat, but with the same features
Colour: shiny metallic
Thickness of gold-coating without Ni-Cu-Ni: 0,05 micro metre
Thickness of whole coating: approx. 12 micro metres
The gold-coating rubs off easily with frequent use. It is therefore suitable for decorative purposes only, not for playing or working.
Chrome (Ni-Cu-Ni-Cr)
Better resistance against rubbing and pressure (that's why we use this coating for our sphere magnets)
Colour: dull, grey-metallic
Thickness: approx. 15 micro metres
Copper (Ni-Cu)
Colour: shiny brown-red-gold. The colour may change over time due to oxidation (darkening, spots)!
Slightly weaker rubbing and impact resistance than Ni-Cu-Ni
Slightly weaker corrosion resistance than als Ni-Cu-Ni
Thickness: approx. 10 micro metres
The copper-coloured surface rubs off with frequent use (similar to gold-coated magnets) and is therefore suitable for decorative purposes only.
Epoxy resin (Ni-Cu-Ni-Epoxy)
(in exceptional cases also just epoxy)
Colour: black
almost 100% non-corrosive, as long as coating is intact
not shock-resistant (crumbles quickly)
Thickness: approx. 10 micrometre
Even the smallest, not visible to the eye, damages of the coating will cause damage to the magnet in the long term when exposed to moisture.
Zinc (Zn)
Colour: matt grey/blueish
only zinc without Ni-Cu-Ni
more susceptible to corrosion than Ni-Cu-Ni
can leave black marks
Thickness: approx. 4 micrometres
Pot magnets
If not noted otherwise, we use neodymium magnets with a Ni-Cu-Ni coating for our pot magnets. The term "coating" in the article description of pot magnets refers to the steel pot around the magnet. In most cases it is nickel (Ni); for the pot magnets that are painted white it is nickel with additional powder coating.
Special coatings
There is a variety of other coatings for neodymium magnets that we do not (or only sporadically) offer in our standard assortment.
Without coating
Naked magnet material, black/grey
Magnets oxidise and corrode quickly when they come in contact with oxygen and water
Magnets need to be covered air- and watertight quickly
We do not recommend having uncoated magnets manufactured.
Silver (Ni-Cu-Ni-Ag)
Shiny silver
Razor-thin coating over normal Ni-Cu-Ni coating, hence the same attributes
Difference purely visual
Material: Sterling Silver
Approx. 12 micrometres thick
Teflon
Grey/anthracite
Only teflon without Ni-Cu-Ni
Nearly waterproof
Very rub-resistant
12-25 micrometres thick
Ferrite magnets: No coating
In theory, you could put various coats on ferrite magnets, but that is technically complex and expensive. The price for the coating would be greater than the price for the whole magnet.
Since ferrite magnets are weather-resistant even without protection, an additional coating is not necessary. Our ferrite magnets are therefore uncoated.
navigation
Contact Person
- Name:
- Elsie Cao
- Tel:
86-571-87785916
86-15355053529
- Email:
- sales04@china-cinfer.com
- Address:
- Marketing Add: 2-11F,Tianda Building,No.180, Genshandong Rd, Shangcheng District, Hangzhou, CHINA
subscription
QR code
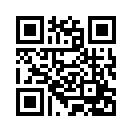